
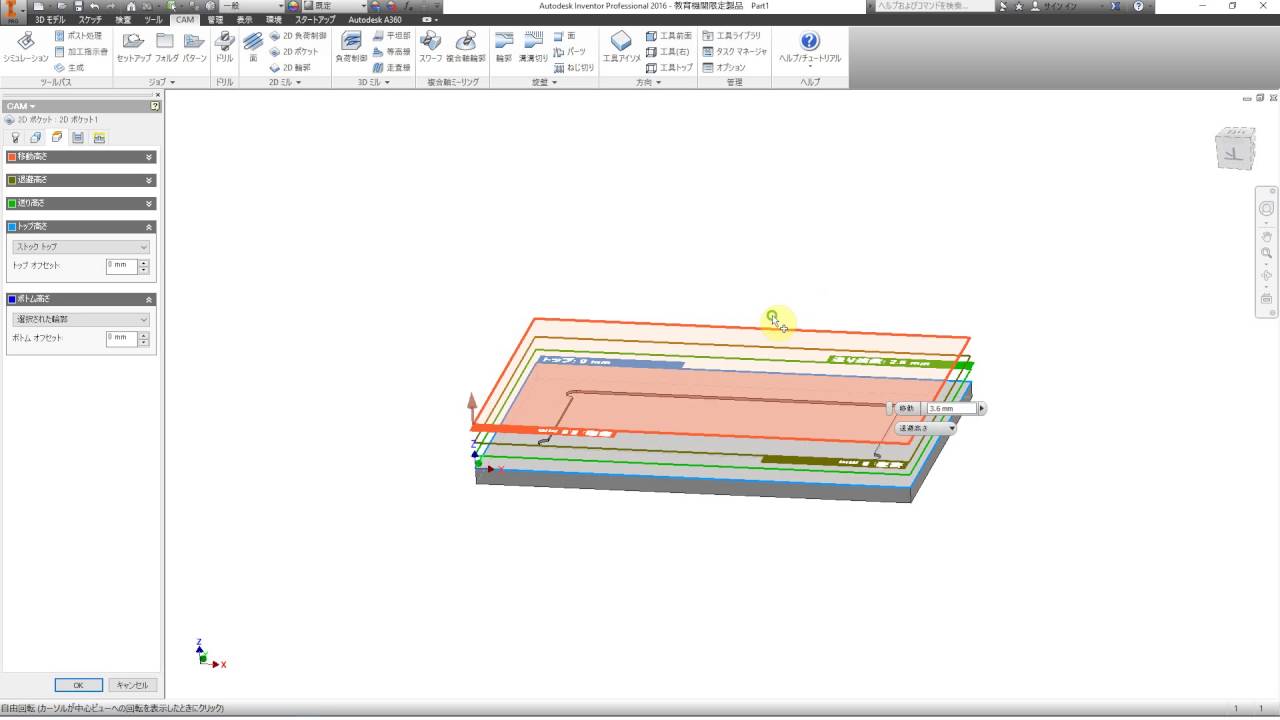
We can actually see this change by clicking “Calculate” at the bottom. This graph also evolves and adapts to changes made to the information above. All the data and information from above is calculated and shown here. Now that we have input all the necessary information, take a look at the bottom of the window and you’ll see a graph. In my example cam I haven’t set any of these values, but here you can set even more options to customize the cam to your specifications.

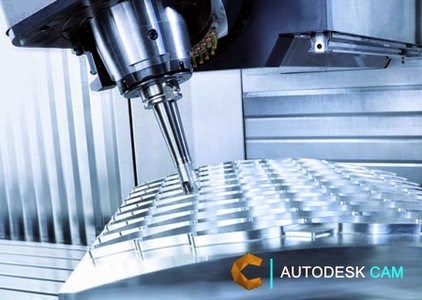
Once we set the value for one, the data for the others will update accordingly.įor users who want to see more advanced settings, take a look at the Calculation tab. In this example I’ve only changed the Lift at End. Here the user can set variables such as: length of the Lift at End, the Max Speed, Max Acceleration, and Max Pressure Angle. There are others as well, but for our basic cam we’ll only need the Roller Radius and Width.įinally, we’ll need to fill out the fields under Actual Segment. The next section pertains to the Follower where we input information such as Roller Radius (rr), Eccentricity (e), and the Roller Width (br). Here we can set the parameters for the cam itself: Start Plane, Basic Radius (ro), and Cam Width (bc). Let’s start in the “Cam” section of the dialog box. Time to dive into how this tool works. You can find the Disc Cam generator by going to Design Tab > Power Transmission > Disc Cam.
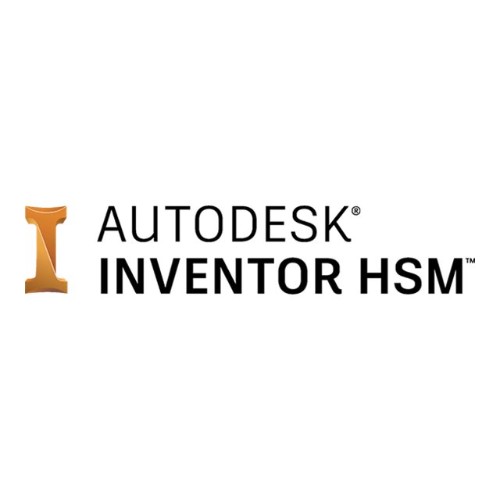
What is the easiest way to create a simple cam in Inventor? Your first response might be: “Just create a sketch outline of the cam using the Spline function and then extrude.” It makes sense right? The problem with the Spline method however, is it has a tendency to not create one continuous smooth edge and create a break in the face of the edge. This can lead to the follower not behaving correctly.Ī better solution is the Disc Cam Generator which creates a fully functioning cam for you in the assembly model along with a separate part file for the cam.
